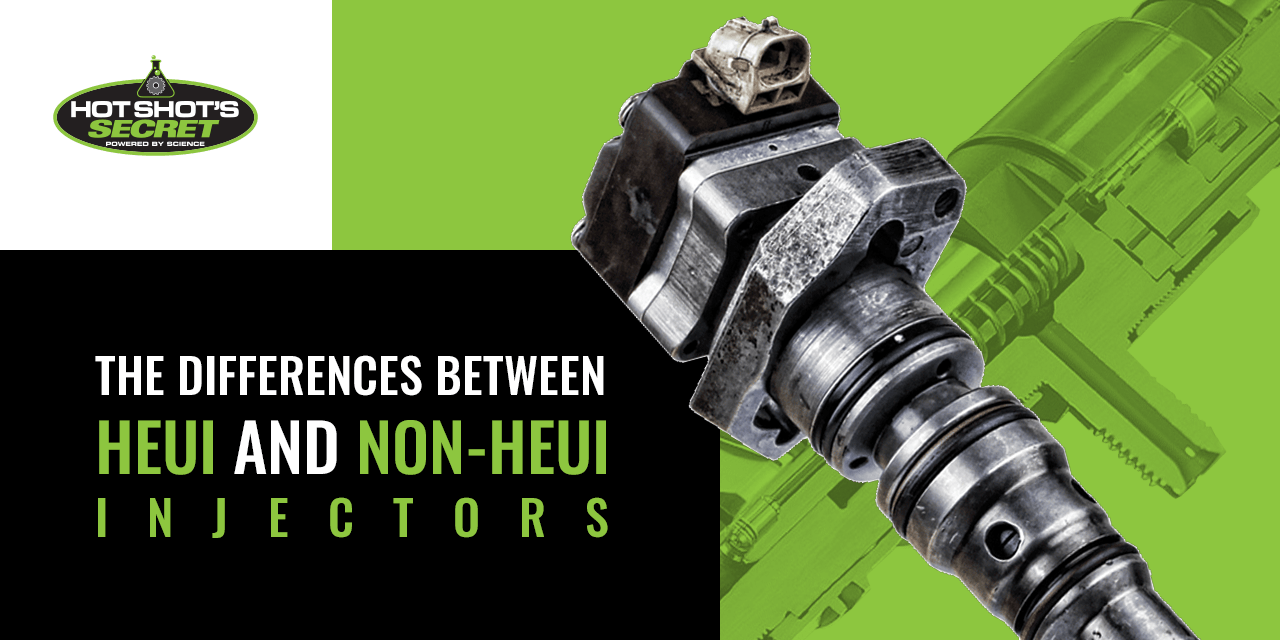
Diesel fuel systems require precise sprays of fuel for reliable, consistent combustion. That’s where injector systems come in. These high-pressure systems send regular streams of fuel to the engine to keep your vehicle running.
There are three primary design concepts for diesel injection systems:
- Mechanical Fuel Injectors (MFIs): This old-school system functions without computer control, firing when the pressure within the system reaches its maximum. Common mechanical injectors include the older Cummins series as well as the Navistar.
- Hydraulic Electronic Unit Injectors (HEUI): This computer-controlled system consists of a combined pump and injector for each engine cylinder. It uses high amounts of pressure to fire precise strokes of fuel to the engine. You’ll mostly find HEUI systems in older Ford Powerstroke injectors.
- Common rail injectors: This computerized system consists of multiple injectors connected to one fuel line, known as a rail. Each injector fires at a different point to send a consistent stream of fuel to the engine. Newer Ford Powerstroke and Cummins injector systems use common rails.
The mechanical-based single-shot system is based on injector pressure and mechanical release while later two-phase systems like HEUI and common rail injectors simply allow the activation of the injection pump to build pressure within the injector, which lifts the check valve and opens the flow of pressurized fuel to spray.
What Are HEUI Fuel Injectors?
What followed was the Hydraulic Electronic Unit Injection (HEUI) system, one of the first designs that revolutionized the clean-burn, quiet diesel engine. As opposed to the earlier single-shot injector design, HEUI systems use computer-controlled hydraulic pressure to supply the injector with high-pressure oil. This building pressure would cause the injector to fire, releasing the fuel.
With the addition of electronic control, the HEUI system enhanced accuracy in injector cycles. The fuel system computer controls the entire stroke cycle, providing much more accurate timing for injection and fuel metering. Additionally, the HEUI system has a higher injection pressure than the previous two-stage injection design.
According to Shane Matt of L and M Fuel Injection Service Inc. in Lafayette, Louisiana, using a computer-controlled system enables the injector to spray more than once per combustion cycle.
Older diesel injectors mechanically injected fuel on top of the piston before hitting top-dead-center (TDC) on the crankshaft. Current injector styles spray a small injection stroke just before the crankshaft hits TDC. This initial stroke is followed by the rest of the fuel upon hitting TDC. The torque generated in this process pushes down on the piston. Optimal force remains and is burned as the crankshaft descends.
Matt claims the system provides much more torque and a quieter engine because it doesn’t cause one big bang before TDC. It’s a smoother, more efficient burn since the majority of combustion takes place during the downward stroke, which creates the extra torque.
And just as HEUI replaced the mechanical pressurization system, the common rail injection system is now in the process of replacing the HEUI system typically found in older Powerstroke engines and DT466E Internationals.
HEUI vs. Common Rail Fuel Injectors
With a common rail injector system, one line, or rail, of pressurized fuel feeds multiple injectors, which all fire at different times. A high-pressure pump supplies up to 35,000 pounds of pressure to the line. The computer then determines the amount of fuel to spray and the timing to do so. Each injector can spray up to five finely atomized strokes per combustion cycle.
This kind of system controls two pilot sprays, one main spray and two post sprays, which means that in addition to the pre-TDC injection, the common rail system may pulse another four times during the downward pass of the piston. These extra sprays provide more torque than an HEUI or mechanical system can.
“With the proper air intake, the common rail system provides a much more efficient burn with nearly 100% ignition,” says Matt.
Piezoelectricity in Injectors
Some newer common rail systems, like the Powerstroke 6.4L and 6.7L, use piezoelectricity, enabling them to function at a higher speed than HEUI or mechanical systems. The term “piezoelectricity,” which literally translates to “pressing electricity,” refers to the electricity passing through crystals under high amounts of pressure.
You’ve seen piezoelectricity in action if you’ve ever seen someone crunching on hard candy in the dark. Crushing the sugar crystals in the candy releases the energy within them, producing electric sparks. A similar thing occurs in fuel injectors, but the crystals remain intact, so they vibrate back and forth, allowing the electrical current to flow through them.
Piezoelectric common-rail injectors are also quieter than their HEUI predecessors, with increased horsepower and torque.
How to Maintain Fuel Injectors
As design specs, more sophisticated components and higher tolerances increase in the evolution of the injectors, so too does the intolerance of contaminated fuel. Matt says that most of the hazards to injectors he sees in his repair service result from dirty, low-lubricity or watered-down fuel. Because diesel fuel naturally contains lubricating compounds, it acts as the sole lubricant for the whole fuel system. For that reason, diesel fuel systems can’t handle contaminated or low-lubricity fuel.
The Environmental Protection Agency (EPA) regulates sulfur levels in diesel fuel. While a lower sulfur level results in a cleaner, higher-performing fuel, it also decreases its lubricity. This happens because the refining process, called hydro-processing, replaces sulfur with hydrogen, a highly reactive substance. The added hydrogen reacts with the compounds in the fuel, removing its lubricating properties and creating a “dry” product that resembles kerosene or jet fuel.
Contaminants can also enter fuel during transport and storage at gas stations. Contaminated fuel can clog up your filters and, if left unchecked, could result in partial or catastrophic engine failure.
Matt advises practicing proper maintenance procedures like regularly changing your fuel filter and additives to avoid premature wear of your fuel system.
“Neglecting the fuel filter can wreak havoc on a fuel system, and additives help increase lubricity, which really extends the life of fuel systems. For example, over the years, our customers that faithfully use Hot Shot’s Secret additives, their fuel systems are in pristine condition, after a longer than usual service life,” says Matt. “We usually see them here with leaks instead of worn hard parts. On the other hand, we have those that use fuel straight from the pump without additives, and a lot of times they are in here earlier than they should be.”
Matt also claims many of his customers who use additives report added economic value due to boosted cetane and “burn-ability” of fuel. Additionally, additives contain cleaning agents that maintain the condition and functionality of your nozzle tips.
“We have noticed a recognizable 25% increase in the longevity of the engine life with proper use of the additives,” says Matt.
Trust Hot Shot’s Secret for Improved Injector Performance
If you’re experiencing problems with your vehicle’s diesel fuel system, we can help. You can use our Diagnose Your Diesel tool to understand what might be causing the issue or shop our site for engine-saving products like oil and fuel additives.