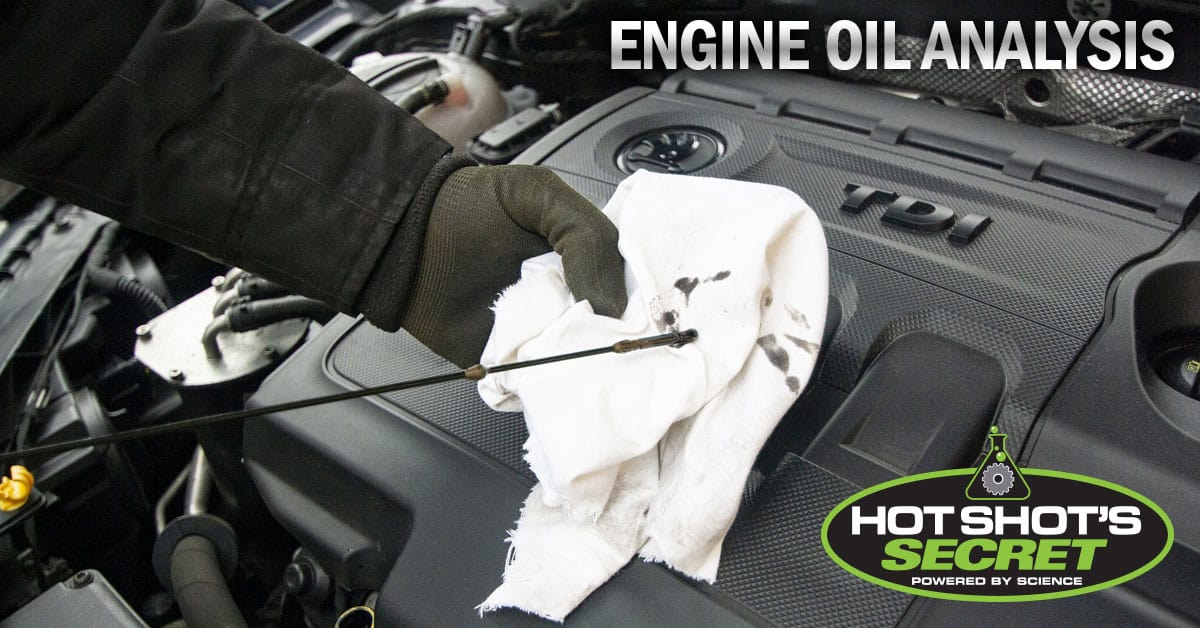
A note from Chris Gabrelcik- Certified Lubrication Specialist (CLS) and Certified Oil Monitoring Analyst (OMA), CEO of Hot Shot’s Secret:
Dr. Roger Dale England, vice president, chief R&D officer, Valvoline, Inc., explains that the primary oil degradation routes are oxidation and nitration. “Today’s engines run hotter and at higher temperatures than older engines, and this increases the stress on the oil. This stress results in the oil oxidizing, and this change precedes other changes that eventually occur, making oxidation/nitration measurements a great leading indicator for optimum oil drain interval calculations.” England cautions that while these are today’s primary measurements, they are not the only data that should be analyzed.”
I agree with Dr. Dale. We have been telling our readers this since 2005 when we started working on the problem with stiction. We found that the oil was oxidizing and baking on the inside of the engine. Cleaning the burnt oil is the first step, keeping it from coming back is the second step. That is how the Blue Diamond Engine oil came to be. We knew the engines were working harder and burning more oil inside the engine. We needed a PAO base oil that would not oxidize to prevent the stiction. Then we added the Frantz Filter to make the whole system more affordable. Having the best oil money can buy is affordable if you leave it in for 50,000 miles.
Examining the future of BN and AN as reliable indicators of oil health in heavy-duty diesel engines running on ultra-low sulfur diesel fuel.
KEY CONCEPTS
• Experts are taking a hard look at the relevance of the acid number and, in particular, base number metrics.
• Current formulation requirements are geared toward oxidation stability and the ability to process contaminants that enter the engine oil from recirculated exhaust gases.
• Testing to detect oxidation and nitration proves to correlate well with the amount of weak organic acids and is a good early predictor of oil thickening.
Almost all the diesel fuel consumed in Europe and the U.S. is ultra-low sulfur diesel fuel (ULSD), which was developed to substantially reduce harmful diesel emissions to promote environmental protection. The significantly lower sulfur content in ULSD has changed today’s diesel engine oil requirements and oil useful life evaluations.
Base number (BN) and acid number (AN) have been widely used as key measurements of engine oil condition. However, monitoring AN/BN becomes a less reliable way to assess oil health in systems running ULSD due to the change in primary acid types in used oil.
Older combustion regimes running on high-sulfur fuel created many strong acids, but with today’s ULSD there are more weak organic acids such as acetic, nitric and formic. These weak organic acids usually are not strong enough to be neutralized by the additive pack base component, making the BN/AN measurement a poor indicator.
While this is true, these organic acids are still strong enough to attack soft metals, often resulting in corrosive wear on both bushings and the solder in heat exchangers. There needs to be a better way to track the oil condition such as Fourier Transform Infrared Spectroscopy (FTIR) for oxidation and nitration detection. Test data by FTIR proves to correlate well with the amount of weak organic acids and is a good early predictor of oil degradation associated with the end of oil life.
STLE-member David Doyle, CLS, OMA I, OMA II, key accounts and special projects, ALS Tribology, explains that today’s North American heavy-duty (HD) diesel engine oil manufacturers are concerned with high oxidation, unacceptable changes in lubricant viscosity, increasing wear and corrosive metal content. Testing for acid number and oxidation are gaining ground as more relevant indicators of engine oil service life than base number in North America. “A high acid number does not mean the engine oil has turned acidic,” he says. “Acid number increases due to reactions with oxidation and oil degradation compounds. Oxidation test results provide a reliable trending parameter that complements other engine oil service life testing well (see New API Categories and Service Life for HD Engine Oils).”
Doyle continues, “Historically, people relied on testing for base number as a key indicator on diesel engine oil service life due to the need of having an alkalinity reserve to combat highly corrosive sulfuric acid. With the significant reduction in sulfur in fuel and engine oil, the relevancy of using base number as a key indicator for service life has been significantly reduced. Formulation requirements today are more concerned with oxidation stability and the ability to handle contaminants that enter the engine oil from recirculated exhaust gases. Today’s engine oils are more concerned with protection from degradation due to oxidation, better detergency and dispersancy.”
Key elements of a ULSD oil analysis program
Dr. Roger Dale England, vice president, chief R&D officer, Valvoline, Inc., explains that the primary oil degradation routes are oxidation and nitration. “Today’s engines run hotter and at higher temperatures than older engines, and this increases the stress on the oil. This stress results in the oil oxidizing, and this change precedes other changes that eventually occur, making oxidation/nitration measurements a great leading indicator for optimum oil drain interval calculations.” England cautions that while these are today’s primary measurements, they are not the only data that should be analyzed.
In regard to oxidation performance, Dr. Alisdair Brown, R&D technical director, Afton Chemical Ltd., says there are many ways oxidation can be measured: from simple laboratory bench tests that can take a few minutes to expensive multi-cylinder engine tests lasting several days all the way to OEM field trials that can take two to three years to complete.
“There’s no single agreed upon best method,” he says. “This can be seen by the proliferation of oxidation bench tests within the industry. This reflects the specific issues observed by OEMs and the individual approaches taken to ensure adequate performance protection. Some of these methods utilize transition metal catalysts to increase severity; others add biofuel to simulate fuel dilution, some with artificial ‘blow-by’, others with oxygen.”
Brown explains that the Sequence IIIH test assesses the extent of oxidation via viscosity increase of the lubricant and the Mack T-13 test, which takes 360 hours and uses roughly 20 gallons of engine oil, tracks oxidation throughout the test by monitoring the increase in oxidation products via infrared spectroscopy as well as any changes in the viscosity of the oil.
“These bench or engine tests are clearly cost- and time-efficient surrogates for in-use operation, so one could take the view that the only way to ensure that adequate protection is maintained is to undertake performance testing in the field,” he concludes.
On a more fundamental level, England cautions that the key to effective used oil analysis is actually using the data. “Our used oil analysis teams consist of local engineers with years of experience with equipment in the field, supported by a dedicated IT team,” he observes. “That tandem allows us to quickly analyze data from any lab, and our local engineers create clear actionable items for our customers to improve their total cost of ownership. There are plenty of other things to worry about in today’s business environment, so we work hard to make sure that maintenance is as easy and cost effective as possible. Used oil analysis is a great tool when the findings are distilled to actionable items that impact profit. If you are paying for this data, make sure you use it.”
Oxidation and antioxidants
According to Doyle, the contributors to oxidation in heavy-duty diesel engine oils are the same contributors in other lubrication applications: heat, moisture and contaminants acting as catalysis, causing oxygen to react with the oil. He explains that, depending on the application, oxidation contributors for in-service diesel engine oil will vary in proportion and relative impact.
“In heavy-duty diesel engine oils, heat and moisture seen under normal operating conditions will contribute to normal oxidation development. Contaminants from recirculated exhaust gases are a contributor, as well as acids from NOx compounds reacting with recirculated exhaust gases and organic acids formed during combustion,” Doyle says.
He continues, “Returning exhaust products from the exhaust gas recirculation to the diesel engine combustion chamber develop nitric acid created by NOx compounds reacting with recirculated exhaust gases. These acids are significantly weaker than sulfuric acid, thus the lessening relevancy of base number and greater relevancy on trending tests for oxidation of the oil for monitoring service life.”
General contaminants from exhaust gases put additional stress on today’s engine oils, Doyle adds, which also has led to enhanced detergency and dispersancy performance in heavy-duty diesel engine oils. “Basically, the oils now have to contend with carrying contaminants that used to leave the vehicle within the exhaust gas.”
Life for antioxidants isn’t easy. Brown explains that antioxidants need to operate effectively under a range of challenging operating conditions, protecting the lubricant, the additive system and the extended operations of the engine. “As such, key characteristics to consider include mechanism of oxidation prevention, thermal robustness and temperature of operation, rate of reaction and low volatility,” he says. “An increasingly challenging consideration is the essential global regulatory compliance of antioxidants and other lubricant additives.”
New API categories and service life for HD engine oils
Dr. Alisdair Brown, R&D technical director, Afton Chemical Ltd., explains that as engines become more efficient through the use of more complex hardware, such as steel pistons and increased turbocharging, the stress per unit volume of oil is increasing. This is compounded as sump temperatures rise and oil drain intervals get longer.
“Put another way, less engine oil needs to work harder for longer,” he says. “This means that formulations need to use higher quality base oils and more effective oxidation control. Further, as we see the increased application of after-treatment devices, and in particular filters, we also see downward pressure on lubricant ash levels. One impact of this is a drive to lower levels of ZDDP to reduce the ash loading.”
A secondary impact of the drive toward lower ash lubricants will be a need to increase the antioxidant loadings to enable after-treatment device compatibility, thus increasing cost. “In addition to being one of the most cost-effective antiwear agents, ZDDP also is a very cost-effective antioxidant,” Brown observes.
So, do these new API categories offer extended service life? Not necessarily, says STLE-member David Doyle, CLS, OMA I, OMA II, key accounts and special projects, ALS Tribology. “Diesel engine oil manufacturers are concerned with maintaining service life that the market and industry have come to expect. But the technical challenge in this is balancing required service life with changing technology and compliance requirements for both engines and the engine oils. What heavy-duty diesel engine oil manufacturers tend to key in on is ‘optimal drain intervals,’ which can vary depending on work environments and service requirements. Heavy-duty engine oils are very robust in regard to handling the increased contaminants they are exposed to in today’s heavy-duty diesel engine applications. These oils hold up their viscosity and lubricity properties very well, which allows them to maintain service life expected of the market and by end-users.”
Brown continues, “Each approved formulation is a carefully balanced mixture of components specific to the application and the design criteria for the fluid. Though oxidation control is an important performance feature, it needs to be addressed as part of the whole performance profile to avoid any inadvertent negative impacts. To ensure that the optimum antioxidant system is defined, one must fully understand the oxidation mechanism in play and tune the specific additives to address these needs.”
Is AN/BN still relevant?
England explains that engines running ULSD produce so much less of the aggressive acids (such as sulfuric) that the base in the oil could react with and neutralize. “The acids we see today are predominantly weak organic acids,” he says. “Our work indicates the base in the oil gets tied up with water from condensation of combustion gases, blocking the reaction with the weak acids. With high sulfur fuel, the strong acids readily react with the detergent micelle core neutralizing the acid. Weak organic acids in USLD engines are not reacting, therefore BN and AN are not the major players they were in years past. BN and AN had their place in the past, but we all are aware of the increased complexity of today’s engines.”
Sulfur has significantly less impact on the creation of sulfuric acid during the combustion process, explains Doyle. “As far as ULSD fuel is concerned, the little bit of sulfur left in the fuel, <15 ppm, serves as an antioxidant; CK-4 engine oil only allows up to 500 ppm sulfur. Higher sulfur in the past mainly contributed to the creation of highly corrosive sulfuric acid. The primary role of higher base numbers in the past was to neutralize the sulfuric acid buildup, which had been the primary factor in engine oil service life. Due to the significant reduction of sulfuric acid, this is no longer a key determinant of engine oil service life.
He concludes, “Thus, the relevancy of base number as a key indicator of diesel engine oil service life is no longer as valid as it once was in regions using low sulfur fuels and engine oils. However, in global regions where higher sulfur engine oils and fuels are still being used, base number will continue to be a key test parameter.”
Reprinted with permission from the September 2020 issue of TLT, the official monthly magazine of the Society of Tribologists and Lubrication Engineers, an international not-for-profit professional society headquartered in Park Ridge, Ill., www.stle.org.